OSHA's Hazard Communicating Regular – The Basics
May 25, 2020

Workplace chemicals can pose a sedate risk to the health and life of workers if not dealt with caution. Most of these chemical-incidental hazards and accidents pass cod to sheer negligence or ignorance by the employees operating theatre the employers. To ensure natural science safety in the workplace, OSHA issued the Hazard Communication Standard in 1983 with a limited setting.
Conforming to the International Standards
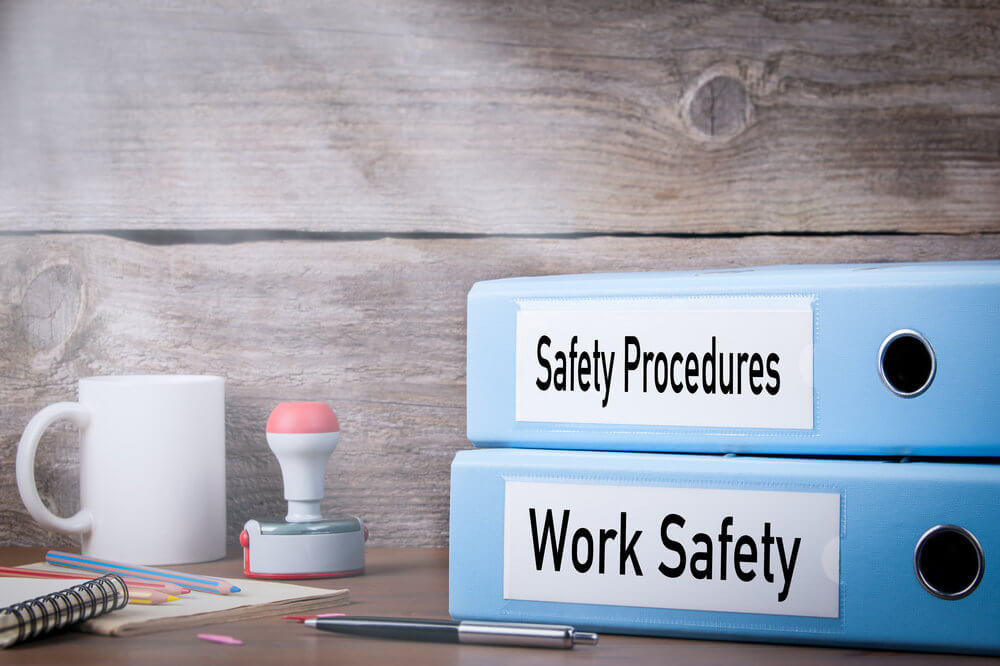
Occupational Safety and Health Administration modified the HCS and broadened the scope to underwrite all industries where workers are possibly exposed to hazardous chemicals. In 2012, the Peril Communication Standard was aligned with the Globally Harmonized Arrangement of Categorisation and Labelling of Chemicals (GHS).
OSHA elucidated that by conforming to the international standards, the comprehensiveness and the uniformity of the HCS wish be improved.
OSHA's HAZCOM is a U.S standard criterial developed to ensure a safe and healthy work environment. Information technology requires employers across all industries to identify the hazardous substances, label them, and civilise their employees about their possible hazards. For instance, companies dealing in hazardous waste handling volition be required to ensure their workers completed the HAZWOPER training broadcast before commencing the work.
The modular also entails employers to follow a formal mechanism that will assistant tell apart the chemical hazards in the work and have requisite management/engineering controls to safeguard the workers from photo. The HAZCOM basic is also called the "Employee Mighty-to-Know" and is described in 29 CFR 1910.1200.
A Formal Hazard Communication Program
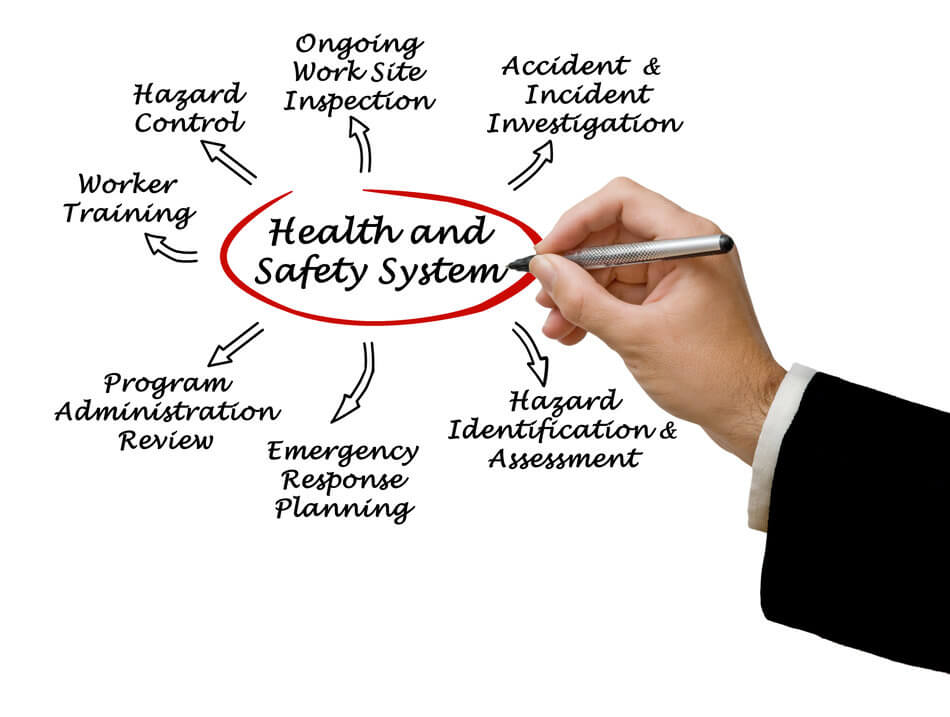
As per OSHA's HAZCOM or HCS regulations, employers must implement a formal hazard communication program that includes – details of chemicals handled, imported operating theatre produced at the work done labels on the containers, safety data sheets (SDSs or MSDSs), a written HCS plan, stuff inventory lists, and an effective training syllabu.
Though implementing HCS regulations is obligatory for organizations, most employers crossways the nation take not been able to practice it to the core. OSHA has cited employers for flunk to enforce the standards, especially the written communicating plan. For the past six years, HCS violations have hierarchical second on the agency's yearly list of most frequent standard violations. Companies failing to comply with the regulations may invite powerful penalties, and flush face imprisonment in case an employee succumbs to injuries attributable stuff exposure.
How to Implement an Effective HCS Program
1. Stock-taking of hazardous materials
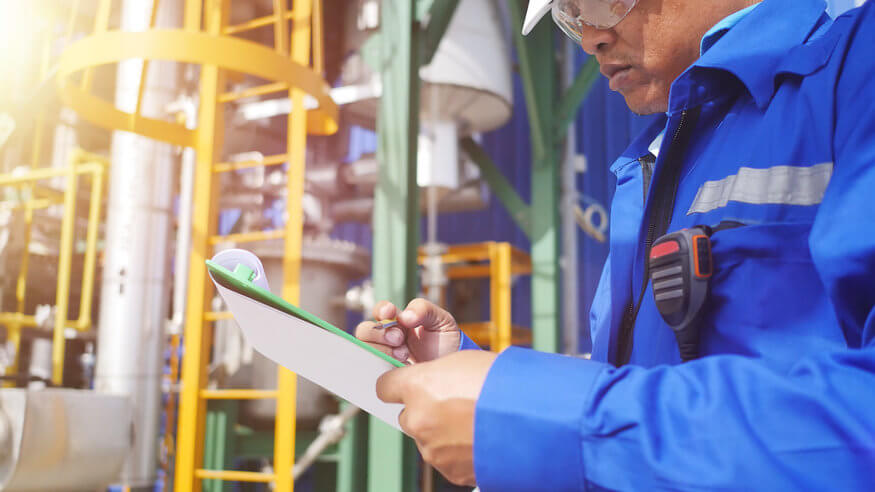
Employers are required to make a name of the hazardous materials existing in their employment expanse. When creating an inventory, IT is essential to check if an SDS is forthcoming for apiece stuff used or handled at the workplace.
An SDS is a scripted OR written material put around a wild chemical. If an SDS is nonexistent, contact the supplier to generate a copy of the same. Until the SDS is received, employers should text file the postulation and record it in a file.
2. System for maintaining SDSs
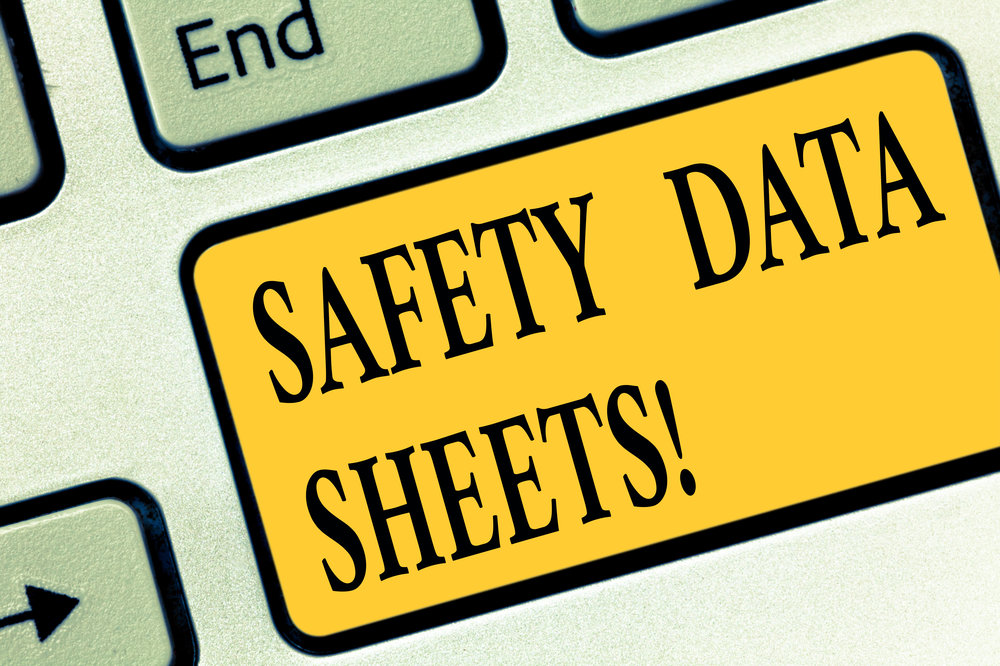
Accordant to the Globally Harmonized System for Classification and Labeling of Chemicals (GHS), SDSs are required to contain 16 sections. This 16-sheet format is aimed at guiding the workers who handle dangerous chemicals about the contents of SDSs. Here's a look at what SDSs should include:
- Sections 1 to 8 should contain general-purpose information about the chemic, its identification, hazards, composition, safe handling practices, and emergency control measures (e.g., firefighting).
- Sections 9 through 11 and 16 need to contain somatogenetic and chemical properties of the chemical, its stability and reactivity selective information, pharmacology information, exposure ascendency information, and its date stamp of preparation or last revision.
- Sections 12 to 15 need to follow consistent per the GHS guidelines but OSHA does not enforce these sections and can exist omitted as they concern matters handled by other agencies. (OSHA Brief)
The information provided in the Refuge data sheets should be easily accessible to anyone in the work.
3. Labels and admonition signs
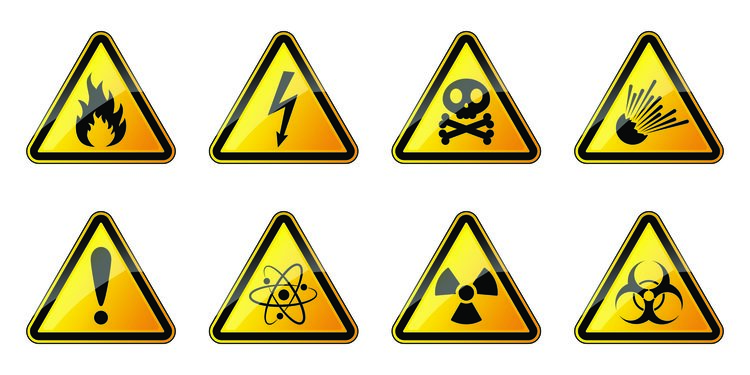
Employers must label the containers of hazardous materials. A label should include –
- The name of the product/material, its other common names Oregon synonyms
- Details of the manufacturing business, importer or other creditworthy parties
- Emergency Ring number
- Use of the chemic
- Jeopardy classification ( e.g., combustible)
- Pictograms or Luck Symbols (e.g., skull and crossbones, flame)
- Hazard statement
- Description of Hazard
4. Training programs
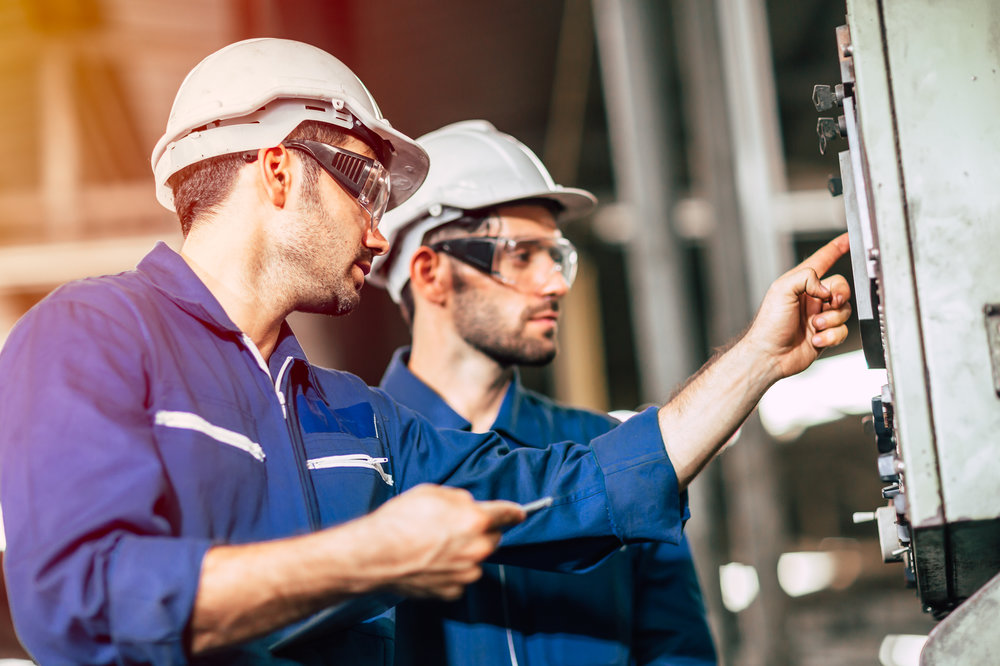
Workers exposed to hazardous chemicals at work should be provided with education and breeding to identify and process safely with hazardous materials before their initial naming. This can be achieved by:
- Conducting group Roger Huntington Sessions to explain SDSs, PPE and what to waste an event of an exposure or material spill
- Through classroom training, mutual courses like OSHA HAZWOPER preparation, etc.
- By training each employee about what chemical(s), he/she would be encountering during the normal duties
- A session on where to find SDSs in the workplace
5. Written hazard communication program
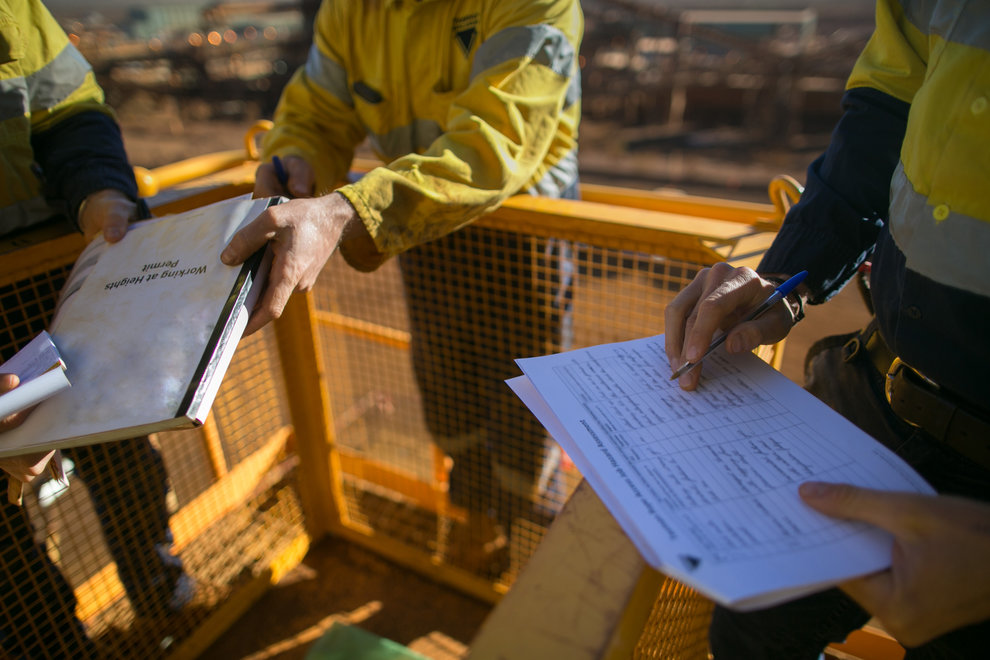
If a company uses operating room produces dangerous chemicals, then the employer is compulsory to maintain a written hazard communication program at the workplace. An employer will be asked to produce this syllabu document during an inspection. This program must include materials inventory, labeling, SDSs, type of training (40 hours HAZWOPER training, classroom, online, conducted past company authorities, etc.). Concisely, a written computer programme should cover everything that is enforced in the workplace and should pronto be obtainable to employees.
Periodic revisions should be ready-made to this political program to address changing work conditions such A when a new PPE is added or a new chemical(s) is handled. IT should be communicated in a way that all employees understand the labeling and symbols connected with a chemical fortune and aware of the risks complex in their handling.
the osha hazcom standard is also commonly called the
Source: https://hazwoper-osha.com/blog-post/oshas-hazard-communication-standard-the-basics/
0 Komentar